Funzionamento/fasi del ciclo

Diagramma della Distribuzione di un motore 2T
1=PMS
2=PMI
A: Lavaggio
B: Scarico
C: Compressione
D: Espansione
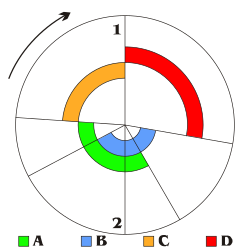
Diagramma della Distribuzione di un motore 2T unidirezionale
1=PMS
2=PMI
A: Lavaggio
B: Scarico
C: Compressione
D: Espansione
Il ciclo termodinamico del motore a due tempi, come noto, si sviluppa completamente in un'unica rotazione dell'albero motore, ma la successione completa delle varie fasi che interessano il fluido motore avviene nell'arco di 2 rotazioni, questo avviene perché il pistone svolge una doppia funzione, come meglio spiegato qui di seguito.
Aspirazione
Il pistone, in salita verso il PMS (
Punto Morto Superiore), crea una depressione nel
carter pompa, e contemporaneamente apre la luce di
aspirazione. Nel caso del
piston port questa apertura avviene con fasatura simmetrica rispetto al
punto morto superiore, con ovvii svantaggi, mentre nel caso della
valvola rotante l'apertura ha una fasatura fissa, ma ottimizzata per il miglior rendimento in un certo campo di regimi di rotazione. È invece la depressione presente nel carter a provocare l'apertura automatica della
valvola lamellare, con fasatura variabile. La depressione (0.2-0.4
bar) richiama la miscela (aria/benzina) fresca dalla luce di aspirazione immettendola nel
carter pompa, che la porterà nel cilindro attraverso le
luci di travaso nella fase successiva.
Pre-compressione e Lavaggio
Durante la discesa del pistone verso il PMI (
Punto Morto Inferiore) avviene la compressione della miscela nel
carter pompa, con un rapporto di compressione compreso tra 1,20:1 e 1,45:1. Nel momento in cui si aprono le luci di
travaso, esaurita l'eventuale sovrappressione residua della fase di scarico, la miscela fresca aria-benzina entra nel cilindro anche grazie alla depressione generata dalla parte iniziale dell'impianto di scarico aiuta il travaso dei gas freschi, durante questa fase parte di questa miscela esce anche dalla luce di scarico, mista a gas combusti.
Compressione
Il pistone, risalendo dal
Punto morto inferiore, occlude dapprima le luci di travaso, poi quelle di scarico. Fra queste due fasi può avvenire una prima compressione a causa dell'onda di pressione riflessa dal controcono dell'impianto di scarico, se questo è del tipo risonante (detto anche "ad espansione" per via della notevole variazione di sezione). In questo caso, una parte della miscela fresca rientra nel cilindro, anche se la quantità intrappolata nel cilindro è inferiore alla cilindrata, perché comunque sia è sempre presente una frazione di gas combusti.
Nella parte finale della compressione la carica fresca viene movimentata dall'anello di
squish, se presente, generando una forte vorticosità che consente una combustione migliore ed un aumento del rendimento termodinamico.
Accensione ed Espansione
L'accensione, avviata da una
candela, avviene con anticipi nettamente inferiori a quelli tipici del 4 tempi, nel caso del
Motore ad accensione comandata, grazie alla forma più razionale della testa permessa dall'assenza delle valvole a fungo. L'eventuale presenza dell'area di squish consente di utilizzare rapporti di compressione molto elevati senza incorrere in fenomeni deleteri, come la
detonazione, inoltre nel 2 tempi è possibile utilizzare un impianto di accensione ad anticipo costante senza una eccessiva perdita di rendimento.
Dopo il PMS (
punto morto superiore) inizia l'espansione, che di fatto si interrompe al momento dell'apertura della luce di scarico, per via del brusco calo di pressione, questo fatto comunque sia non determina una perdita notevole di rendimento rispetto ad un motore a 4 tempi di pari cilindrata, visto che il motore a quattro tempi richiede un'apertura anticipata delle valvole di scarico, pressoché paragonabile al due tempi. Con il passare degli anni la luce di scarico dei due tempi si è via via ridotta, a favore di una sua estensione nel senso trasversale, in modo da guadagnare corsa utile e avere un rendimento sempre maggiore, del tutto paragonabile a quello dei quattro tempi.
Scarico
In fase di discesa il pistone scopre la luce di scarico. L'espulsione dei
gas combusti avviene per semplice differenza di pressione, e non per l'azione di pompaggio del pistone come nel 4 tempi. Lo scarico risuonante, se presente, rende più veloce questa fase, grazie alla depressione sviluppata dal primo tratto dello stesso, permettendo di ridurre l'altezza delle luci di scarico e aumentare il rendimento.
In alcuni casi (motori con aspirazione lamellare e condotto che collega direttamente il vano della valvola ai condotti di lavaggio) questa depressione può addirittura influire sul "rapporto di lavaggio", ovvero aumentare la quantità di gas freschi che entrano nel cilindro.
Tipologia di Lavaggio/funzionamento [modifica]
Il lavaggio (o travaso) del cilindro con i gas freschi, nei motori a due tempi, avviene secondo varie scuole di pensiero:
Flussi incrociati

Motore a due tempi a flussi incrociati
Questo tipo di motore (CrossFlow in inglese) ha due luci, una di scarico e una di travaso, poste ai lati opposti del cilindro, con il pistone munito di deflettore, per evitare che i due flussi (gas di scarico e miscela fresca) si mescolino, quindi la carica fresca va verso la testa grazie alla forma del deflettore, mentre i gas combusti escono.
Questo è stato uno dei primi sistemi di lavaggio utilizzati nella produzione, ma ha avuto vita breve per via delle complicazioni indotte dal deflettore, che aumenta il peso del pistone, aumenta la superficie esposta alla combustione e rende difficile disegnare una camera di combustione ottimale.
Correnti tangenziali
In questo tipo di lavaggio (Loop-scavenged in inglese), si studiano le varie posizioni e direzioni delle luci e condotti di lavaggio per avere un risultato ottimale ed eliminare la necessità del deflettore. In pratica queste luci sono disposte in direzione opposta alla luce di scarico, imponendo perciò alla miscela fresca di salire verso la testa, invertire la direzione e raggiungere lo scarico soltanto dopo aver effettuato questa "giravolta", da cui il nome inglese. Spesso viene denominato lavaggio "Schnürle" dal nome dell'ingegnere tedesco,
Adolf Schnürle, che lo inventò nel
1925. Inizialmente pensato per i motori diesel della
KHD, venne ceduto in licenza esclusiva alla DKW. Il sistema di lavaggio a correnti tangenziali si è ampiamente diffuso dapprima in Germania e dopo la seconda guerra mondiale, nel resto del mondo. Attualmente è il tipo di lavaggio più utilizzato nei motori moderni ad accensione comandata, mentre non è più utilizzato sui motori ad accensione spontanea, sostituito dal ciclo unidirezionale.
Strutture particolari
Il motore a ciclo loop è stato proposto in alcune particolari e controverse configurazioni, che più o meno si discostano come struttura da un motore classico.
Questo tipo di motore riprende in parte i vantaggi del motore con pistoni a doppio diametro, ma il pistone ha una forma tradizionale.
La sua peculiarità è di avere al posto delle bielle delle aste, che vengono azionate direttamente dall'albero motore secondo uno schema insolito ad aste, dove ogni asta è dotata di un sistema di tenuta che isola la camera in cui si muove il pistone dal carter, quindi la "pompa di lavaggio", in questo caso, è costituita dalla parte inferiore del pistone, dal cilindro e dall'asta e relativa tenuta. Il rapporto di pre-compressione è più alto, rispetto al sistema con
carter pompa, ma il "rapporto di lavaggio" (rapporto fra volume di gas freschi immessi nel cilindro e volume del cilindro) sarà più basso a causa della minore cilindrata della pompa rispetto alla camera superiore, in quanto alla cilindrata occorre sottrarre il diametro dell'asta di comando del pistone moltiplicato per la corsa. C'è il vantaggio di avere l'imbiellaggio ben lubrificato, dato che è isolato dalla camera-pompa di lavaggio, ma è anche vero che questo sistema non consente regimi di rotazione molto elevati, visti i pesi notevoli delle parti in moto alterno e della complessità del sistema di azionamento delle aste.
L'ammissione della carica fresca alla camera-pompa può essere regolata da uno qualsiasi dei sistemi già visti, invece per quanto riguarda l'immissione della carica fresca nel cilindro, si può seguire sia lo schema a flussi incrociati che il
loop.
Lavaggio unidirezionale

Classico esempio di un moderno motore unidirezionale
Questo tipo di lavaggio (Uniflow-scavenged in inglese) è utilizzato principalmente sui motori
Diesel due tempi, ma può essere utilizzato anche per motori ad accensione comandata. Nel caso di un motore con una struttura classica (generalmente nella configurazione diesel), l'immissione della carica fresca non avviene tramite i travasi, ma tramite una o più valvole a fungo e l'iniettore posti sulla testata del motore, mentre l'espulsione dei gas combusti avviene sempre tramite le luci di scarico poste nella parte bassa del cilindro, ma questa tipologia di motore esiste anche in una configurazione inversa.
Il nome è dato dal fatto che il flusso dei gas freschi va dalla testa del motore alla luce di scarico quasi in linea retta, limitando così la possibilità di miscelazione con i gas combusti, inoltre ha come secondo vantaggio la possibilità d'utilizzare un carter a bagno d'olio o a secco, dove l'olio non è a contatto con il carburante, un motore di questo tipo è il 2T Diesel navale Wärtsilä-Sulzer RTA96-C della
Wärtsilä, che ha un rendimento superiore al 0,5 o 50% (risultando uno tra i migliori).
Una variante di questo tipologia di motore (poco usata) si utilizza il carter come pompa di lavaggio, quindi si hanno le normali luci di travaso e carter pompa e dove lo scarico avviene tramite una o più valvola/e a fungo posta/e sulla testata, questa configurazione perde il vantaggio della lubrificazione, dato che in questo caso l'olio deve essere miscelato con il carburante.

motore a 2 tempi a stantuffi contrapposti
Un altro tipico caso di lavaggio unidirezionale si ha nel
motore a 2 tempi a stantuffi contrapposti ideato da
DKW (generalmente nella configurazione
ad accensione comandata), dove i due alberi motore sono sfasati opportunamente, in modo da iniziare a scaricare prima che si aprano le luci di lavaggio e da chiudere i travasi per ultimi, in questo modo la "pompa di lavaggio" può attuare una reale sovralimentazione.

motore a 2 tempi a cilindri paralleli
Un'altra struttura di questo ciclo è il
motore a due tempi a cilindri paralleli, ideato da
Garelli-Marcellino-
Isomoto, dove si avevano due cilindri paralleli formati d un unico elemento, una testa che metteva in comunicazione i due cilindri e formata anch'essa in un unico pezzo, dove un cilindro aveva la luce di scarico e l'altro permetteva l'ingresso di carica fresca al carter-pompa ed era munito di almeno un travaso, inoltre i pistoni erano vincolati all'albero motore tramite una sola biella a "Y".
[4]
Questa disposizione permetteva d'avere i due pistoni leggermente sfasati tra loro, permettendo d'avere un'apertura anticipata della luce di scarico rispetto alla luce del/i travaso/i e una chiusura posticipata di questi rispetto alla luce di scarico, senza il problema della sfasatura dei due alberi motore, che porta a una perdita di rendimento termico, dato che il tutto veniva gestito da un solo albero motore.
Il
motore a 2 tempi a cilindri paralleli con pistone di lavaggio è stato ideato da
DKW è un motore che permette una lubrificazione indipendente dalla miscela fresca e avere un motore a cilindri paralleli costruito in modo semplice rispetto a quanto verrà fatto in seguito dalla
Garelli-Marcellino-
Isomoto.
[5]Un'altra struttura di questo ciclo è il
motore a due tempi a cilindri convergenti, ideato da
DKW, dove si avevano due cilindri che convergono in un unico punto, in modo da ridurre il volume della camera di combustione, una testa che metteva in comunicazione i due cilindri e formata anch'essa in un unico pezzo, dove un cilindro aveva la luce di scarico e l'altro permetteva l'ingresso di carica fresca al carter-pompa ed era munito di almeno un travaso, inoltre i pistoni erano vincolati ognuno a un suo albero motore, i quali erano vincolati tra loro tramite un sistema a ingranaggi creato direttamente sullo spallamento dell'albero motore e che vincolava a far ruotare i due alberi in direzioni opposte, inoltre con questo motore si utilizzava una pompa di lavaggio diversa dal carte pompa, esattamente come nel motore a cilindri paralleli.
[6]A scalinata o con pistoni a doppio diametro
Il
motore a scalinata (Stepped Piston Engine in inglese), utilizza una tecnica particolare per l'aspirazione e distribuzione della carica fresca nel cilindro del motore, che consiste nell'avere un cilindro complementare e relativo pistone che aspira e distribuisce la carica dentro ad altri due cilindri, dove avviene la combustione, per poter alimentare due cilindri questo pistone (che ruota allo stesso regime degli altri due) ha due camere, di cui una è formata dalla testata, cilindro e pistone, mentre la seconda è formata dal cilindro, pistone e carter.
[7]
Per regolare il flusso della carica fresca nel cilindro complementare si può utilizzare la semplice tecnica del piston port, una luce centrale al cilindro che viene aperta solo quando il pistone è alle estremità e alimentare la camera opposta a quella momentaneamente utilizzata, mentre per il flusso diretto a uno dei due cilindri dove avviene la combustione il flusso è governato dal semplice movimento del pistone che apre o chiude le luci dei travasi.
Il vantaggio di questo sistema è che il pistone è più facilmente lubrificabile e possono essere utilizzati cuscinetti come su un motore a quattro tempi. I brevetti su questo disegno sono detenuti da Bernard Hooper Engineering Ltd (BHE).
L'evoluzione di questo sistema è l'utilizzo di pistoni a
doppio diametro, dove si può avere anche un solo cilindro che è a diametro differenziato, ovvero hanno una zona superiore normale ed una zona a diametro maggiorato più in basso (vicino all'albero motore) e anche il pistone è forgiato nello stesso modo, in questo modo la funzione di pompa di lavaggio viene svolta dall'insieme cilindro-pistone maggiorato a fianco, mentre la parte superiore a diametro ridotto funziona come un normale 2 tempi.
[8] È evidente che i due pistoni devono avere gli angoli di manovella sfasati di 180 gradi.